I'm very particular about wiring. When I see someone that uses wire nuts, or those stupid scotch locks everywhere it just makes me want my own wiring job to be absolutely perfect. So that is what I have set out to do. I want room to expand, and want everything to be weatherproof as-well as neat and tidy looking. So here it goes.
I started off with a few hundred dollar worth of parts from Waytek wiring. Super cheap prices for high quality products. Too good to be true? Sort of... You must order in bulk. That's why I have so many of each part. Can never have too many though I suppose.

The main important components include a Cooper Bussman Fused power distribution block. It has room for 10 fuses and 5 micro relays. It can supply up-to 80 amps per bus continuously. It is all weather sealed with a cover.

Molex MX 150L plugs. I wanted to use plugs so everything could be easily added too, removed, taken out, etc... These seemed up to the job. I chose this model of plugs because they were weather sealed, and also had panel mount receptacles. With the panel mount option, The receptacle could be permanently mounted my "wiring hub thingy" (designed in later pics) for a much neater appearance and easier use.



Cole Hearse 100 Amp circuit breaker. This will be the breaker between the battery and the cooper bussman distribution center. The breaker also has a manual trip button so I can easily disconnect the entire distribution block and all aftermarket wiring/accessories from power with a click of a button. That way I don't have to remove the battery ground.
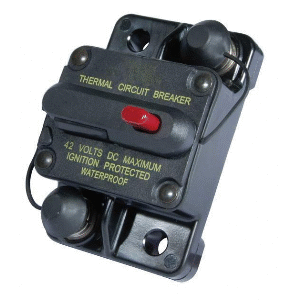
I needed a place to mount everything. I decided that between the core support and the drivers battery would give me:
1. Ample room to mount and work
2. Close to battery (short battery cables)
3. Somewhat near hole in fire wall
4. Somewhat protected from direct salt/water spray
5. Ability to be removed
I needed a panel to mount my main Fuse block and all the plugs.
Being an Aluminum welder/fabricator has its perks for sure! After a few hours taking measurements and building a drawing in autocad, I was ready to cut. I used the Computerized plasma cutter on a piece of .100 aluminum. It took a few tries to get the fit perfect and all the pieces in optimum locations but I was satisfied with my third go around.


Main components test fit. Holes still need to be drilled. I will make a template on autocad and print it out so I get the holes in the exact places.


35 amp Micro relay in place just for fun.

Roughed into place.

I am now at the stage where I need to mount it to the core support. I want it to be easily removable so I will end up welding on some studs to the aluminum panel. I will then drill and tap the studs so all I have to do is unscrew a couple screws with a philips and unplug my handy dandy molex plugs and the entire aluminum panel comes right out if I every need to service something under neath it or add another circuit for an accessory. Kinda hard to explain so you will have to wait until I can get it done to see what I have in mind.
Here is the other half to my wiring endeavor. The cab! Thanks to Tousley Ford, I got an F-650 dash for 17.95 and freight for only ~$10. Score!
Cut gauge holes. I could have fit three, but didn't like how close they were to each other so I went with two. I will figure out something to put in the empty space in the future. A carling switch panel was installed after cutting out the top space as well.


Paint mixed by my local body shop and sprayed with areasol paint spray gun by me, myself, and I! I also had OTRATTW.com make me some custom rocker switches. These guys are awesome! High quality switches with literally any symbol or text you can think of! The top light is on with my dash lights, while the bottom LED is lit when the switch is "on"

Soldered in blue LED's and resistors in the top light socket and Red LEDs in the bottom socket.

Installed. The amp guage is just a place holder. I had it sitting in a drawer from an old A model Kenworth. Eventually I will put a fuel pressure gauge in its place.
